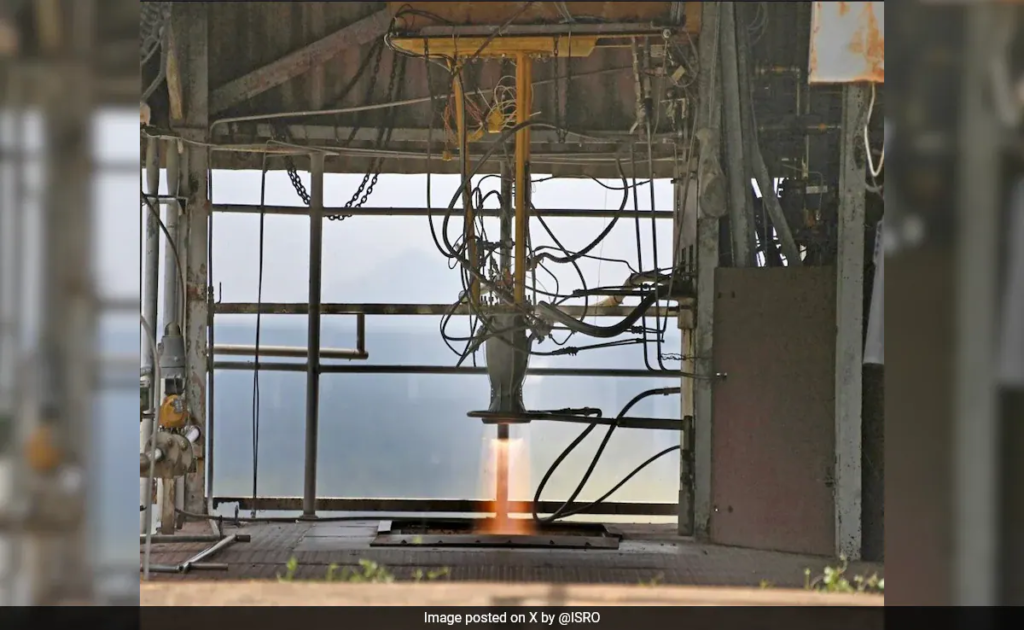
The Indian Space Research Organisation (ISRO) has marked a significant milestone by successfully testing a 3D-printed liquid rocket engine for its Polar Satellite Launch Vehicle (PSLV). This innovative step not only advances rocket manufacturing technology but also aligns with sustainable practices by saving a substantial amount of raw materials and cutting down production time.
The engine tested is the PS4, which is crucial for the PSLV’s upper stage operations, helping deliver satellites into Low-Earth orbit. Traditionally manufactured through machining and welding, the PS4 engine’s transition to 3D printing, or additive manufacturing, was executed by WIPRO 3D, a leader in metal additive solutions within India.
The advantages of switching to 3D printing for this engine are significant:
- It utilizes the Laser Powder Bed Fusion method, which reduced the number of engine parts from 14 to just one, streamlining both the design and production processes.
- Material efficiency is dramatically increased, reducing metal powder usage drastically compared to traditional manufacturing methods.
- The engine, using Nitrogen Tetroxide and Mono Methyl Hydrazine in a pressure-fed mode, successfully underwent a full qualification test lasting 665 seconds at the ISRO Propulsion Complex in Mahendragiri, Tamil Nadu.
The successful deployment of this technology not only showcases ISRO’s commitment to innovation but also sets a new benchmark for future developments in space technology. This advancement promises to enhance the efficiency of satellite launches, making space more accessible and sustainable. The 3D-printed PS4 engine is expected to be integrated into the standard PSLV program, marking a significant shift towards more advanced, reliable, and environmentally friendly rocket technology.
Leave a Reply